Automotive battery control unit (BCU)
Reliably calculate battery states, run BMS housekeeping, and communicate with the domain controller
The battery control unit (BCU) calculates battery states, performs BMS housekeeping, and communicates with the domain controller. It includes the master controller, power management IC, communication interfaces, transceivers, and memory for logs. The BCU runs the BMS software, driving monitoring units, collecting values, and calculating battery states (SoC, SoH, SoP, SoS), while updating firmware.
Maximize efficiency with battery control units (BCUs)
Infineon offers a wide portfolio of controllers catered to different needs of the automotive applications.
- Cores: TriCore™ based core up to 6 CPUs
- Qualification: AEC-Q 100 up to Grade 0 (Ta ≤ 125°C)
- Functional safety: ISO 26262 ASIL-D
- Memory: Up to 16 MB flash, 6.6 MB SRAM
- Security: HSM EVITA Full
- Software: AUTOSAR-compliant MCAL drivers available
TRAVEO™ microcontroller family
- Cores: Up to dual core Arm® Cortex® M7
- Qualification: AEC-Q 100 up to Grade 1 (Ta ≤ 125°C)
- Functional safety: ISO 26262 ASIL-B
- Memory: Up to 8 MB flash, 1 MB SRAM
- Security: HSM EVITA Full
- Software: AUTOSAR-compliant MCAL drivers available
Reliable and compact power solutions for automotive BCUs
- Integrated boost functions prevent system blackouts during battery voltage fluctuations.
- Low quiescent current minimizes standby power consumption in always-on functions.
- Compliant with AEC-Q100 standards, ensuring robust performance and system safety.
- Meets the latest network interfaces
- Support in a small form factor for TRAVEO™ T2G, AURIX™, and PSoC™ MCU families.
OPTIREG™ PMIC (TLF35584QVVS1: For 5 V -μC; TLF35584QVVS2: For 3.3 V -μC)
- Integrated multi-rail power supply solutions for safety-critical applications
- Efficient voltage regulation with various architectures (DC-DC, linear, tracking regulators)
- Additional monitoring and supervision features for comprehensive system control
OPTIREG™ PMIC (TLF11251LD)
- Integrated half-bridge capable of 2.5 A
- Enables the usage of OPTIREG™ PMIC TLF35584 with high-end second-generation TriCore™ AURIX™ 32-bit microcontrollers TC38x/TC39x.
Other products
- S6BP20x series: One-channel buck boost DC-DC converters
- S6BP501A and S6BP502A: 3-channel output PMICs with buck and boost converters, providing 5.0 V, 3.3 V, and 1.2 V power sources
- S6BP401A: Single-chip power management solution with 6-channel power output, reducing PCB size and bill of materials
Ensure seamless transmission with communication transceivers
The transceivers enable the battery control unit (BCU) to communicate with the domain controller for
- Calculating battery states (SoC, SoH, SoP, SoS)
- Cell balancing
- Pack thermal management
- Triggering disconnection and alerts when needed
- House keeping
Infineon provides a wide variety of CAN and LIN transceivers that meet the needs of BCUs.
Reliable monitoring data transmission with isolated devices
All monitored parameters, such as voltages, temperatures, and currents need to be transmitted to the main controller (BCU) for battery state calculations and housekeeping. However, while the ECU often sits in the low-voltage domain, the cell monitoring units sit in different high-voltage islands that must be kept isolated at all times.
Wired BMS topology: Infineon provides isolated-UART transceiver solutions with exceptional robustness for both capacitive and inductive isolation. The iso-UART supports complicated cell topologies by enabling high-speed communication across many daisy-chained monitoring devices. For additional robustness, redundant ring daisy-chaining ensures continuous communication even if a link breaks. CRC-protected data frames complement communication robustness.
Wireless BMS topology: Alternatively, to meet the even higher requirement of isolating CMBs, a wireless transceiver is a perfect solution. Infineon offers a set of automotive-grade Bluetooth devices that support Bluetooth® LE-connected mesh, offering superior network availability and communication bandwidth.
Ensuring safety, optimize charging, and increase lifetime
The BMS records vital parameters such as voltage, current, temperature, and others throughout the battery lifecycle, even when the battery is switched off, to fulfill the following functionalities:
- Immediate derivation of information on actual cell capacity, SoC, SoH, power consumption (charge/discharge), remaining operating time of cell, etc.
- Later extraction of typical mission profiles. Together with advanced machine learning algorithms, the battery could be tuned for performance or proactively preconditioned when an acquired load scenario occurs.
- As a flight recorder-like black box that continuously records all relevant battery data to trace the root causes of malfunctions, clarifies warranties in case of (hazardous) incidents or simply support new business models based on the "pay-per-use" principle.
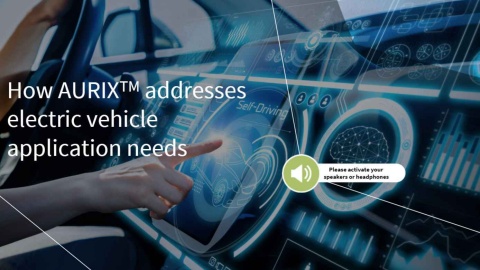
Training topics:
- Get to know how AURIXTM is able to answer the needs of the electric vehicle market
- Recognize and explore how AURIX™ TC3xx addresses key electric vehicle challenges, and understand the main features of the AURIX™ TC3xx microcontroller

In this training you will:
- Understand what a battery management system is
- Recognize the main advantages that Infineon AURIX™ microcontrollers can bring to these systems