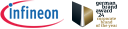
Overall, three projects out of 24 have been nominated. A jury of independent experts from science and industry selects the nominees and the winners.
Even the nomination for the “Deutscher Zukunftspreis” is considered as highest recognition for technology and innovation in Germany. Our team of high-frequency radar chips is among the three nominated teams.
Driving has become increasingly safer over the years, and radar technology is the next leap forward. The last few decades have already seen a considerable decline in the number of road traffic accidents that result in severe or fatal injuries. This trend began with the introduction of passive safety systems such as ABS (1978), frontal airbags (1980), and side airbags (1996). Now, active safety systems are bringing further advances. These systems warn the driver or actively intervene in the driving process, so avoiding or minimizing the effects of a crash. Examples of this type of safety system include pedestrian detection, distance warning and blind spot assist. Many of these active safety systems employ radar technology in the form of chips that send and receive electronic waves in an extremely high frequency range. Compared to other, mostly camera-based, driver assistance technologies, radar functions reliably in any situation – even in difficult visibility conditions caused by snow, fog, heavy rain or dazzling backlight.
In driver assistance systems, cameras and radars are the systems of the future. Also because of the complexity in sensor fusion, it is likely that radar and image signals will be combined, because this enables practically all critical driving situations to be covered.
Mercedes Benz first installed a distance radar system in 1998, in its S-Class range. At that time, the costs for manufacturing the necessary high-frequency components were extremely high. What's more, the material required for the semiconductors was expensive and difficult to process. The upshot of this was that radar technology was initially restricted to premium-class vehicles. Even at the time, Infineon was convinced of the potential of this technology for enhancing active safety, and spent years researching new solutions that would overcome the technical constraints of the time. Eventually, two innovations led to a breakthrough: the manufacture of silicon germanium-based (SiGe) sensors and use of the new eWLB packaging technology. Thanks to these innovative manufacturing processes, the new radar systems became affordable for all drivers. A technology that was previously reserved for the owners of premium vehicles thus came to be used for active crash prevention in cars of all classes. In the meantime, emergency brake assist systems are available as inexpensive optional extras even in small cars, often costing less than a metallic finish.
Radar operates on the basis of high-frequency electromagnetic oscillations sent out as millimeter waves. 77 Gigahertz (GHz) radar technology processes 77 billion oscillations per second, that's over 30 times more than the highest frequencies used in mobile communications. Up to 2009, only semiconductors based on gallium arsenide (GaAs) were able to process frequencies as high as this. However, the manufacturing processes for GaAs chips are far less mature than those for silicon-based chips and therefore more expensive. A further disadvantage is the lower level of integration, i.e. fewer functions can be placed on the surface of GaAs chips. In 2009, after many years of R&D work, Infineon became the first company able to develop highly-integrated circuits for this frequency range based on silicon and silicon germanium (SiGe) – the materials most frequently used for semiconductor manufacturing. This made it possible to employ the same sort of standard production techniques as are used for the mass manufacturing of memory, logic and microprocessor components. What's more, instead of the eight GaAs chips previously required, the Infineon team was able to compress a wide range of the radar module functions onto a maximum of two SiGe components. This innovative leap opened the door to a mass market.
The next decisive breakthrough was the idea of applying technology from the mobile communications domain to car radar – eWLB (embedded Wafer-Level Ball Grid Array). At first, industry experts were not convinced that the eWLB technology would be able to meet the automotive sector's high reliability requirements. The Infineon team, however, remained optimistic and continued with their research work, funded by the German Federal Ministry of Education and Research. Eventually, in close collaboration with the customer Bosch, a solution was found. Today, instead of delivering the naked chip, Infineon encloses it in a robust package. The benefits for the customer are two-fold. Firstly, the component is eminently capable of meeting the requirements in the high frequency range. Secondly, inexpensive standard techniques can be used for further processing. All in all, maximum performance at a minimum overall cost.
Further development of the SiGe and eWLB technologies for use in radar systems has given Infineon a competitive lead of around two to three years over its rivals in the USA and Asia. R&D work for these technologies was performed in Munich, Regensburg, Linz and Dresden. The radar systems themselves are manufactured entirely in Germany. All stages of the process – from chip manufacturing to processing in the package – are carried out at Infineon's plants in Regensburg and Dresden. These facilities are able to ensure the quality necessary for car safety systems and, at the same time, keep the costs as low as possible thanks to innovative manufacturing processes.
The SiGe and eWLB technologies have enabled radar systems to move from the premium segment to the mass market. Demand is now growing worldwide: the market for 77 GHz radar systems has jumped from around half a million in 2009 to approximately 7 million in 2015. By 2020, market analysts expect demand to climb to around 19 million systems.
Radar systems make cars safer and more efficient. After systems that assist drivers, the next step is the deployment of autonomous driving solutions, in which radar systems will also play a critical role. In January 2015, an Audi A7 completed the journey between San Francisco and Las Vegas practically without the intervention of a driver. 150 self-driving Google cars are already on the road, and gathering practical experience. Using radar technology from Germany.
Last update: November 2016